Quality control is the backbone of a thriving manufacturing industry. It ensures that the products meet the desired standards, providing credibility to businesses and assurance to customers. As the world moves toward a more digitized and automated future, Quality Control Devices are becoming increasingly crucial in maintaining product integrity.
This comprehensive guide explores the pivotal role of these devices in the quality control process, shedding light on their functionalities, types, and benefits. As we delve deeper, you will discover how these devices can revolutionize your business operations, ensuring consistency, efficiency, and quality in every product that rolls off your production line. So, let’s navigate the world of Quality Control Devices together, shall we?
Understanding Quality Control
Quality control devices: An essential cog in the machinery of excellence In the grand theatre of manufacturing and production, quality control devices play a role that is as pivotal as it is unassuming. These devices are the unsung heroes, diligently working behind the scenes to ensure that the products we use meet the highest standards of quality, safety, and efficiency. Quality control devices encompass a wide variety of tools, machines, and software, all designed to measure, test, and monitor the quality of products during the manufacturing process.
From simple tools like measuring tapes and gauges to more complex devices like infrared thermometers and spectrophotometers, these devices ensure that every product that rolls off the assembly line is nothing short of perfect. The importance of these devices cannot be overstated. They provide manufacturers with a clear and quantifiable understanding of their product’s quality, enabling them to identify and rectify any issues or imperfections.
This not only ensures the delivery of top-notch products but also helps in maintaining a brand’s reputation and customer loyalty. In the fast-paced and competitive world of manufacturing, quality control devices are the gatekeepers of excellence. They are the quiet sentinels, ceaselessly working to uphold the stringent standards of quality that we, as consumers, have come to expect and rely on.
So, the next time you marvel at the impeccable quality of a product, spare a thought for the humble quality control devices. They may be out of sight, but their impact is certainly never out of mind.
Definition of Quality Control
Quality control devices are indispensable tools in the industry, designed to maintain the integrity of a product or service. They act as vigilant gatekeepers, ensuring that each product meets the desired standards and specifications. Simply put, these devices are the superheroes of the production line, tirelessly working to eliminate defects and guaranteeing the “quality” in quality control.
They are the silent custodians of brand reputation, making sure that customers always receive the best. Quality control devices, therefore, play a pivotal role in fostering trust, enhancing customer satisfaction, and ultimately, driving business success.
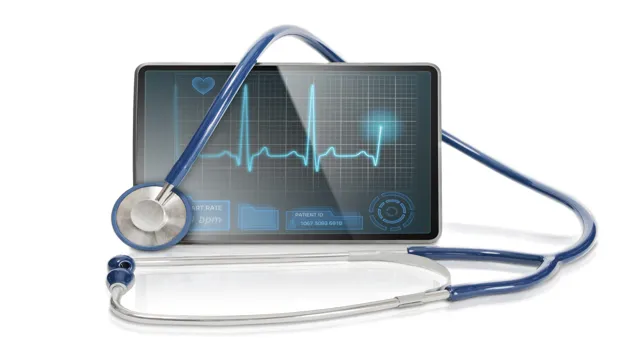
Importance of Quality Control
Quality control devices play an integral role in maintaining product excellence, preventing defects, and ensuring customer satisfaction. These indispensable tools enable businesses to consistently meet industry standards, thereby fostering trust and loyalty among consumers. With their ability to identify discrepancies early in the production process, quality control devices not only save resources but also safeguard a company’s reputation.
In essence, they serve as the gatekeepers of quality, ensuring that every product that leaves the production line is nothing short of perfect. The importance of these devices, therefore, cannot be overstated.
Exploring Quality Control Devices
Quality control devices – the unsung heroes of product manufacturing. They work tirelessly behind the scenes, ensuring that each and every product that leaves the production line meets the requisite standards for consistency, safety, and performance. These devices come in various forms, each designed meticulously to gauge different aspects of a product’s quality.
For instance, there are devices that measure dimensions to ensure precise sizing, while others test material strength to confirm durability. Some devices even monitor color consistency to guarantee the visual appeal of the product. Without these diligent devices, it would be nearly impossible to maintain the high standards that consumers have come to expect.
They enable manufacturers to identify and rectify errors early in the production process, saving time, resources, and potentially, the company’s reputation. In a world that constantly seeks perfection, quality control devices are the silent watchdogs. They scrutinize every minute detail, ensuring that what we consume or use is of the best possible quality.
So, the next time you marvel at the impeccable finish of a product, remember to silently thank these quality control devices for their indispensable role in the manufacturing process. In the realm of production, these devices are not just tools; they are the gatekeepers of quality, the guardians of consumer trust, and the catalysts for business success.
Types of Quality Control Devices
Quality control devices are the unsung heroes of manufacturing, ensuring that the products we consume meet the required standards. These devices range from simple tools like calipers and micrometers that measure size and thickness, to complex machines like spectrophotometers that analyze color and light. There are also coordinate measuring machines (CMMs) that examine the geometric features of an object, and non-destructive testing (NDT) equipment that checks for hidden defects.
These devices, with their precision and accuracy, are the guardians of quality, silently working behind the scenes to maintain the integrity of our beloved products.
Functions of Quality Control Devices
Quality control devices are the unsung heroes in the manufacturing industry, ensuring that every product meets the highest standards of perfection. Their primary function is to meticulously inspect and evaluate products, identifying any defects or deviations from the specified quality standards. They also play a crucial role in monitoring production processes, providing critical feedback that helps in minimizing errors and enhancing overall product quality.
All in all, these devices are like vigilant watchdogs, tirelessly working to keep substandard products at bay and guaranteeing that consumers always receive products of the highest quality.
Choosing the Right Device
Navigating the world of quality control devices can be a bit like finding a needle in a haystack. With a plethora of options available, making the right choice may seem daunting. However, armed with the right knowledge, you can make an informed decision that best suits your needs.
From ensuring precision and accuracy to optimizing efficiency, the right quality control device is instrumental in safeguarding your product’s integrity. In this blog, we will take you on a journey, exploring various quality control devices, their features, and how to choose the one that fits your requirements to a tee. So, buckle up and get ready to become a savvy chooser of quality control devices.
Case Studies of Quality Control Devices
Section Title: Examining Real-World Applications of Quality Control Devices To fully understand the impact and significance of quality control devices, we must delve into real-life applications that illuminate their value and effectiveness. In this section, we will navigate through a series of compelling case studies that showcase the diverse ways in which these devices are deployed across various industries. From the meticulous lens of medical equipment manufacturers to the high-speed production lines of automobile factories, quality control devices are paramount in ensuring that all products meet the necessary safety and performance standards.
We will explore how these devices help in catching potential defects early, saving companies from costly recalls and reputation damage. In the food and beverage industry, we’ll see how these devices play a pivotal role in maintaining the consistency of the products and meeting strict health regulations. In the digital technology sector, we’ll look at how quality control devices aid in delivering flawless user experiences, thereby boosting customer satisfaction.
Every case study will offer a unique perspective, unraveling the intricacies of quality control devices and their indispensable role in shaping the quality and safety of products we use daily. Prepare to be intrigued and enlightened as we embark on this journey of exploring the unseen heroes of the manufacturing world – the quality control devices.
Quality Control in Manufacturing
In the world of manufacturing, quality control is the heartbeat that drives success. The use of quality control devices is paramount in ensuring consistency, efficiency, and reliability in the production process. These indispensable tools meticulously scrutinize every product, detecting any discrepancies that may compromise the end product’s integrity.
They are the unsung heroes, the vigilant watchdogs on the manufacturing floor, ensuring that the products not only meet but surpass the set standards. In essence, quality control devices are the ultimate gatekeepers, safeguarding brand reputation and customer satisfaction in the manufacturing industry.
Quality Control in Food Industry
In the food industry, quality control devices play a pivotal role in ensuring that the products reaching consumers are safe, high-quality, and compliant with regulations. These nifty gadgets, often inconspicuous in their operation, perform essential functions such as detecting contaminants, monitoring temperature, and measuring portion sizes. They are the unsung heroes, tirelessly working behind the scenes, upholding the integrity of our food supply chain.
Without them, maintaining consistent high-quality food production would be akin to cooking a gourmet meal in the dark. So, next time you enjoy a meal, spare a thought for these quality control devices, the silent guarantors of your food’s safety and quality.
Future of Quality Control Devices
Section Title: Navigating the Future Landscape of Quality Control Devices As we delve deeper into the era of technological advancement, quality control devices are undergoing revolutionary transformations. These devices, once confined to rudimentary checks and balances, are now evolving into sophisticated tools, powered by cutting-edge technologies such as artificial intelligence, machine learning, and predictive analytics. The future of quality control devices is set to be dominated by smart, autonomous systems that can detect and rectify defects with efficiency and accuracy that were unimaginable a few years ago.
Real-time monitoring, predictive maintenance, and automated decision-making are just a few of the game-changing features these futuristic devices promise. Moreover, the integration of cloud computing and big data is enabling these devices to store and analyze vast amounts of data, facilitating more informed decision-making. These advancements are ushering in a new era of quality control, characterized by increased productivity, cost-effectiveness, and reliability.
In this brave new world, quality control devices are no longer just tools; they are strategic assets that can significantly enhance a company’s competitive edge. However, harnessing their full potential requires a shift in perspective and a willingness to embrace change. In the end, the future of quality control devices is not just about technology; it’s about how we adapt to this technology to drive growth and innovation.
So, buckle up and get ready for a thrilling ride into the future of quality control devices, where possibilities are as vast as our imaginations.
Emerging Technologies in Quality Control
In the ever-evolving world of manufacturing, the advent of advanced quality control devices is transforming operational processes. These emerging technologies offer innovative solutions for maintaining product standards, enhancing efficiency, and reducing wasteful errors. From AI-powered inspection systems to IoT-enabled monitoring devices, these tools are redefining the traditional norms of quality control.
The integration of these technological marvels promises not only improved product quality but also a significant boost to production efficiency. So, brace yourself for a quality control revolution that is set to redefine the industry benchmarks!
Impact of AI on Quality Control
The advent of Artificial Intelligence (AI) has revolutionized various industries, but its impact on quality control is particularly noteworthy. Quality control devices, powered by AI, have not only enhanced the accuracy of inspections but have also increased efficiency. These smart devices can identify defects and inconsistencies with unmatched precision, reducing human error significantly.
Furthermore, AI-enabled devices can analyze vast data sets rapidly, enabling swift decision-making processes. Thus, the integration of AI into quality control devices has transformed the industry, ensuring superior quality products, improved customer satisfaction, and increased profitability.
Conclusion
In conclusion, quality control devices are the unsung heroes in the manufacturing process. They are the vigilant guardians that ensure no subpar product leaves the production line, the silent whistle-blowers that uncover any faults or defects. They are the embodiment of the saying “measure twice, cut once”, ensuring precision, consistency and reliability of the final product.
Indeed, having them in the production process is like having a seasoned chef in the kitchen, making sure every dish is cooked to perfection. So, the next time you marvel at the flawless design of a product, remember it’s not just the work of skilled craftsmen or advanced machinery, but also the vigilant eyes of quality control devices.
Frequently Asked Questions [FAQs]
What are quality control devices?
Quality control devices are tools and instruments used to ensure that products or services meet specified quality standards. They are used to measure, test, and monitor the consistency, reliability, and functionality of products or processes.
What is the role of quality control devices in manufacturing?
In manufacturing, quality control devices play a crucial role in ensuring the end product meets the desired quality. They are used to check the consistency of materials, monitor production processes, detect defects, and facilitate corrective actions. This helps in minimizing errors, reducing waste, and enhancing customer satisfaction.
Can you give some examples of quality control devices?
Examples of quality control devices include calipers, micrometers, gauges, thermometers, optical inspection systems, digital scales, and hardness testers. More advanced devices include automated robotic systems and software programs for data analysis and visualization.
How do quality control devices contribute to cost efficiency?
Quality control devices contribute to cost efficiency by detecting defects early in the production process, thus reducing rework and waste. By ensuring the production of high-quality products, these devices also help avoid the costs associated with warranty claims, returns, and damage to the company’s reputation.
What industries commonly use quality control devices?
Quality control devices are used across a wide range of industries including manufacturing, food and beverage, pharmaceuticals, automotive, aerospace, electronics, and many more. Any industry that values consistency, reliability, and quality in its products or processes will likely utilize quality control devices.
How has technology impacted the development and use of quality control devices?
Technology has greatly impacted the development and use of quality control devices. With advancements in technology, these devices have become more accurate, reliable, and efficient. Automated systems and software have allowed for real-time monitoring and analysis, reducing the need for manual inspection and increasing overall productivity.
Leave a Reply