In the bustling world of industrial operations, machinery safety guards stand as the unsung heroes, offering a robust shield between the operators and potential hazards. These pivotal components of any industrial workspace not only ensure the well-being of your workforce but they also amplify productivity by minimizing mishaps. However, a comprehensive understanding of these safety guards is often overlooked, leading to compromised safety standards.
This blog will delve into the intricate world of machinery safety guards, highlighting their importance, functionality, and the precautions required to enhance industrial safety. By unraveling the complexities of these defensive apparatuses, we aim to foster a safer, more efficient industrial environment that prioritizes employee security above all else.
The Importance of Safety Guards
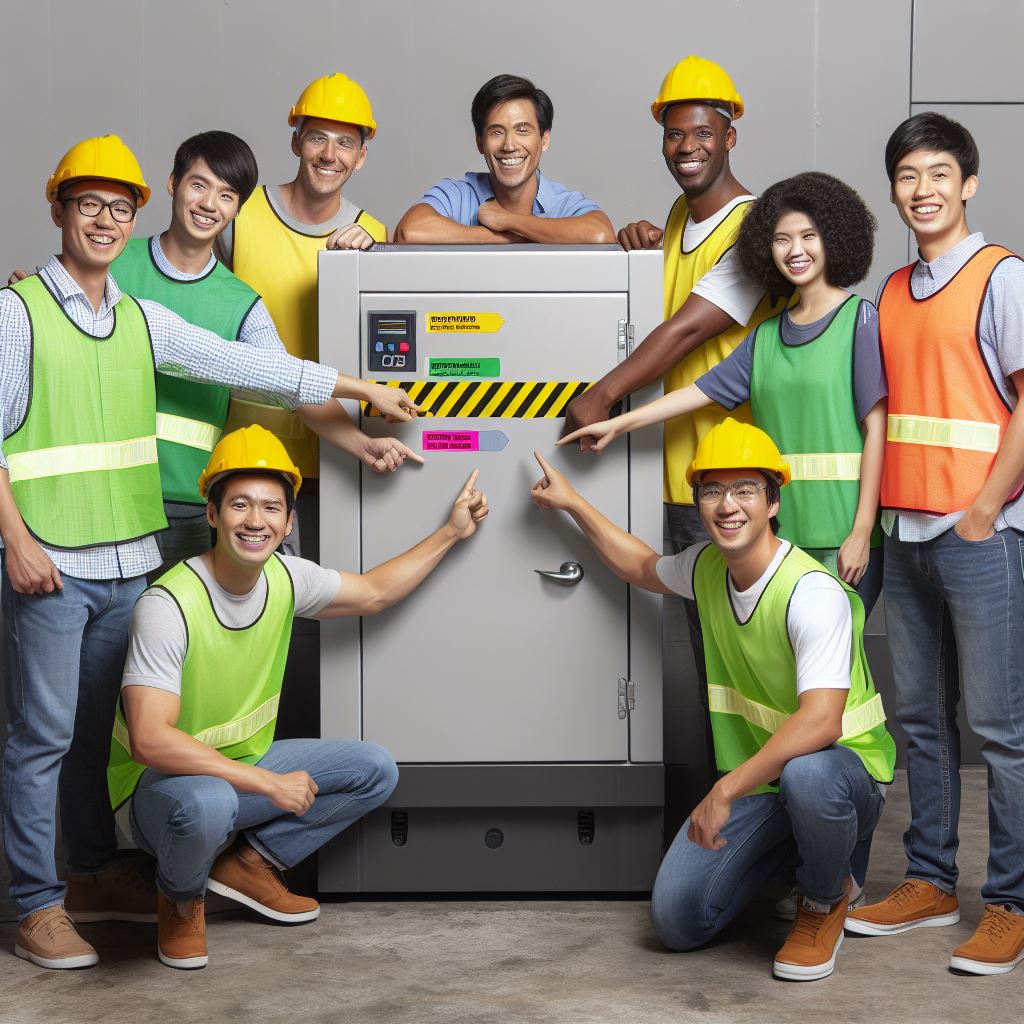
In the realm of industrial operations, machinery safety guards are not just an optional accessory; they form an integral part of the safety protocol. Imagine playing a high-stakes game of chess without a queen. That’s akin to operating heavy machinery without appropriate safety guards.
They function as the protective shield, intercepting any potential harm that could befall the operator. Machinery safety guards are the unsung heroes of industrial safety. They quietly do their job, reducing risks and preventing accidents, much like a vigilant goalkeeper in a soccer match, protecting the goalpost from any unwelcome intrusions.
They form the first line of defense against potential hazards that can result from machine operation such as flying debris, sparks, or even accidental contact. Their importance transcends mere physical protection. The psychological reassurance that these guards provide to machinery operators is priceless.
Knowing that a robust safety measure is in place allows workers to focus on their tasks without being burdened by safety concerns. This not only enhances productivity but also fosters a safe and secure work environment. In essence, machinery safety guards are the stalwart knights of industrial safety, silently standing guard and ensuring that the machinery kingdom operates smoothly and safely.
Investing in them is not just a regulatory requirement, but a commitment to the well-being of your workforce. So the next time you see a piece of machinery, remember to acknowledge the steadfast guard that stands by it, protecting and serving.
Preventing Accidents with Guards
Implementing machinery safety guards is a proactive approach to creating a safer work environment. These protective barriers serve as the first line of defense, shielding personnel from potential hazards associated with moving parts of machinery. Not only do they protect workers from inadvertent contact, but they also prevent flying debris, sparks, and splashes of hazardous materials.
By employing machinery safety guards, businesses can significantly minimize the risk of accidents and injuries, fostering a culture of safety while also complying with regulatory standards. Indeed, the use of safety guards is a mark of a responsible, safety-conscious organization.
The Role of Guards in Compliance
Machinery safety guards play an integral role in maintaining compliance with workplace safety regulations. These unsung heroes of the factory floor do more than just prevent accidents; they are an essential part of a much larger system. By effectively shielding workers from the raw power of industrial machinery, they ensure that businesses adhere to stringent safety standards.
Hence, these humdrum-looking machinery safety guards are the silent sentinels, ensuring a harmonious balance between productivity and safety, while keeping the compliance inspectors content. So, let’s tip our hard hats to these guardians of compliance and safety.
Types of Safety Guards for Machinery
Understanding the Different Types of Machinery Safety Guards Machinery safety guards are an essential component of any industrial or manufacturing setting. They are designed to protect operators and other employees from potential hazards associated with machinery operation, such as moving parts, flying debris, sparks, and excessive noise. However, it’s important to note that not all machinery safety guards are created equal.
There are different types designed for specific applications and machinery. The most common type is the fixed guard, which is permanently attached to the machine. These guards are typically used in areas with minimal operator interaction, providing a robust and permanent barrier between the operator and the machine parts.
Adjustable guards, on the other hand, offer flexibility. They can be moved or adjusted to accommodate different sizes of material or to allow closer proximity to the machine during setup or maintenance tasks. Then there are interlocked guards, designed to shut off or disengage the machine when opened or removed.
This type is ideal for machinery that requires frequent access during operations. Lastly, we have self-adjusting guards. These automatically adjust to the size and shape of the material being inserted into the machine, offering optimal protection without compromising productivity.
Choosing the right machinery safety guards involves a keen understanding of your machinery, processes, and the tasks performed by your operators. By making an informed choice, you can ensure a safe and efficient work environment, safeguarding both your employees and your business.
Fixed Guards: An Overview
Fixed guards are the unsung heroes of machinery safety, acting as steadfast barriers between workers and potential hazards. These stalwart protectors, commonly known as machinery safety guards, are a crucial aspect of any industrial work environment. They are designed to provide an impenetrable shield, ensuring the moving parts of any machinery remain out of harm’s way.
Fixed guards offer an effective, no-nonsense solution to safeguarding employees, reducing downtime caused by accidents, and fostering a culture of safety within the workplace. Indeed, a well-guarded machine is a testament to the value placed on human life in the industrial setting.
Interlocked Guards and Their Uses
Interlocked guards are an invaluable device in the realm of machinery safety, acting as vigilant gatekeepers for users. These guards are ingeniously designed to automatically shut off or disengage a machine when the guard is opened or removed, ensuring the safety of operators. Often utilized in manufacturing and industrial settings, they serve to prevent accidents and injuries that could result from contact with moving parts, flying debris, or sparks.
Thus, interlocked guards are not just a smart addition to your machinery, but essential assets for maintaining a safe and productive working environment. This ingenious invention is indeed a testament to the adage, “Prevention is better than cure.”
Adjustable Guards: Pros and Cons
Adjustable machinery safety guards are an indispensable component in any industrial workspace, ensuring the safety of employees while enabling efficient operation. These versatile fixtures offer a host of benefits, including customization to suit varying machine sizes and types, improving accessibility and maintenance ease. However, they also present some drawbacks.
Their adjustability can potentially compromise safety if not properly managed and they may require frequent checks to ensure optimal functioning. Despite these challenges, the benefits of adjustable machinery safety guards far outweigh the cons, making them a worthy investment for any business prioritizing worker safety and operational efficiency.
Installation and Maintenance of Guards
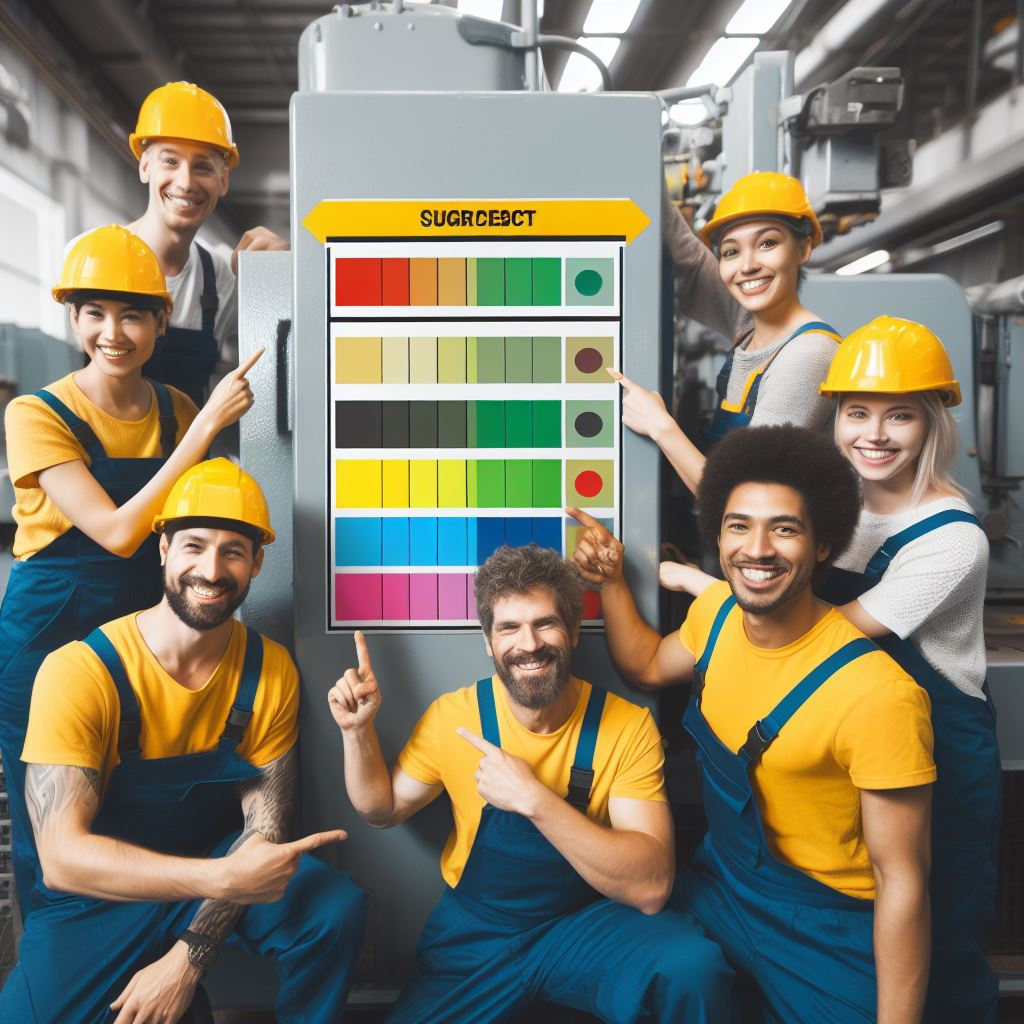
Section Title: The Intricacies of Installing and Maintaining Machinery Safety Guards Machinery safety guards are the unsung heroes of the industrial workspace, silently protecting employees from accidents and injuries. These vital components are essential to maintaining a safe and productive atmosphere, but their installation and maintenance is not always as straightforward as it may seem. Installation of machinery safety guards requires a keen eye for detail and a deep understanding of the machinery’s operational mechanisms.
These guards must be positioned to provide maximum protection without interfering with the machine’s functionality. The process demands precision, patience, and a high degree of technical knowledge. Once installed, the real work begins.
Regular maintenance of these safety guards is pivotal to their efficiency. This involves periodic inspections to check for wear and tear, timely replacements, and ensuring that they remain securely affixed to the machinery. A poorly maintained safety guard can be just as hazardous as not having one.
Investing time and effort in the proper installation and maintenance of machinery safety guards is not just about compliance with safety regulations. It’s about creating a workspace that prioritizes the well-being of its people. After all, a safe workplace is a productive one, and machinery safety guards are at the heart of this equation.
Effective Installation Techniques
Installing machinery safety guards effectively requires meticulous planning and execution. It’s not just about bolting a barrier in place, but rather, carefully assessing the machinery and understanding the potential risks. This includes identifying moving parts, pinch points, flying debris, and other potential hazards.
Once these risks are identified, the right safety guards can be selected and strategically installed. This might involve using adjustable or self-adjusting guards, fixed guards, or interlocked guards, depending on the machine’s design and function. The key is to ensure maximum safety without hampering the machine’s operation – a clever balancing act that requires expertise and precision.
Maintaining Safety Guards
Ensuring the longevity and effectiveness of machinery safety guards is imperative in creating a secure working environment. Regular inspections, timely replacements, and comprehensive cleaning are just a few maintenance practices that can enhance the safety quotient. A well-maintained safety guard not only safeguards the machine but also boosts the productivity of the workforce.
Thus, the significance of machinery safety guards cannot be overstated. Keeping them in top-notch condition is not just a safety measure, but a smart business move. After all, a stitch in time, especially in the realm of machinery safety, indeed saves nine!
Safety Guards: Legal Requirements
Compliance with legal requirements is crucial when it comes to the installation and use of machinery safety guards. These essential devices are not just a savvy investment for safeguarding your machinery; they serve as a protective shield for your workforce, preventing accidents and potential liability. According to the Occupational Safety and Health Administration (OSHA) in the United States, employers are legally required to provide their employees with a work environment free from recognized hazards, which includes the provision of machinery safety guards.
These guards are designed to prevent contact with dangerous moving parts, control hazardous energy, and protect against flying debris. In the United Kingdom, the Provision and Use of Work Equipment Regulations 1998 (PUWER) stipulates that all machinery should have suitable guards in place and maintained to ensure safety. The Canadian Centre for Occupational Health and Safety also emphasizes the importance of machine guards in preventing worker injuries.
Remember that each machine may require a specific type of guard, designed to provide optimal protection while not hindering the machine’s operation. It’s not simply about having guards in place; it’s about having the right guards, correctly installed, and routinely inspected. In a nutshell, machinery safety guards are not just a box to tick on your compliance checklist.
They are a testament to the value you place on human life and well-being, a silent reminder of your commitment to safety. So, don’t just guard your machines; guard the heart of your operation – your people.
Frequently Asked Questions (FAQs)
What are machinery safety guards?
Machinery safety guards are protective devices designed to prevent contact with moving parts of a machine, thus ensuring the safety of the operator and other workers in the vicinity.
Why are machinery safety guards important in an industrial setting?
Machinery safety guards are essential in an industrial setting to protect workers from potential hazards, such as cuts, burns, or crushing injuries that can occur due to contact with moving parts. They also help prevent accidents that can lead to equipment damage and work stoppages.
What are the different types of machinery safety guards?
There are several types of machinery safety guards, including fixed guards, interlocked guards, adjustable guards, self-adjusting guards, and perimeter guards. The type of guard used depends on the machine and the nature of the task being performed.
How do I ensure that machinery safety guards are being used effectively?
To ensure effective use of machinery safety guards, regular inspections and maintenance should be conducted. This includes checking for damage, ensuring the guard is correctly fitted and is not interfering with the operation of the machine, and training employees on the importance and correct use of the guards.
Are there any standards or regulations regarding machinery safety guards?
Yes, there are numerous standards and regulations regarding machinery safety guards. For example, the Occupational Safety and Health Administration (OSHA) in the U.S. has set specific requirements for machine guarding in the workplace. It’s crucial for businesses to comply with these regulations to ensure worker safety and avoid penalties.
How can machinery safety guards impact productivity?
While some may view machinery safety guards as a hindrance to productivity, the opposite is actually true. By preventing accidents, they can reduce downtime caused by injuries and equipment damage. Furthermore, they can enhance worker confidence, leading to more efficient operation of the machinery.
Conclusion
Machinery safety guards are like the unsung heroes of the industrial world, discreetly ensuring the safety of operators and protecting the machinery from potential damage. They are the knight in shining armor for the damsel in distress, the superhero to the city in danger. Always remember – the absence of a safety guard may result in a thrilling story of survival, but its presence guarantees a long, uninterrupted story of productivity and safety.
So, let’s raise a wrench to these silent guardians, these watchful protectors – our safety guards!
Leave a Reply